Operations Jan 2, 2020
How a Change to Food Inspectors’ Schedules Can Make Our Food Safer
Yes, they try to be objective. But seemingly small quirks in their schedules can affect their judgment.
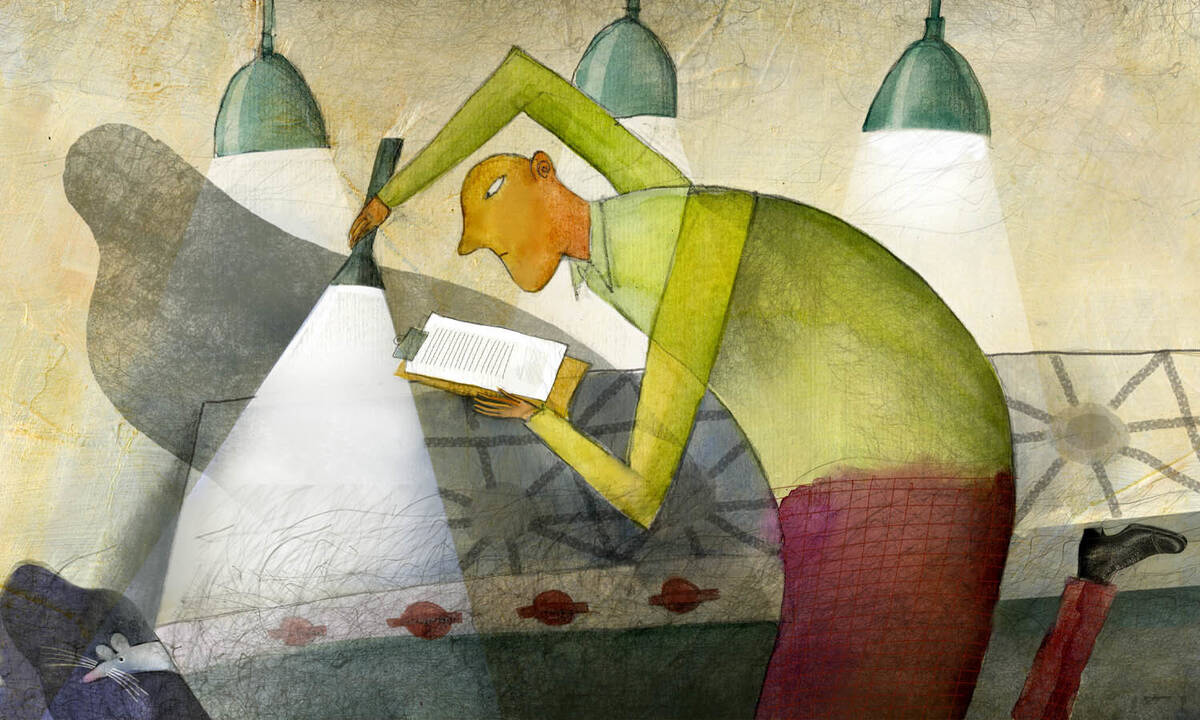
Yevgenia Nayberg
Food-safety inspectors are sticklers by design.
They follow rigorous processes and use objective evidence to identify health violations. So their work would seem to be as immune to human error as any regulatory job could hope to be. Still, hundreds of thousands of potential violations go uncited each year, putting people at additional risk for foodborne illness.
While no inspection process (or inspector) is perfect—are there certain common factors that could be compromising the quality of inspectors’ work?
Maria Ibanez, an assistant professor of operations at Kellogg, hoped behavioral science could shed some light on the question. Ibanez’s research focuses on how task scheduling affects decision-making, so she naturally wondered if the order in which inspectors conduct their site visits affects how many violations they cite.
“I believe it’s really important to understand how people are affected by the sequence of tasks they have to complete at work. That gives us an opportunity to improve performance by being smarter about scheduling,” she says.
She and Michael Toffel of Harvard Business School analyzed thousands of health-inspection reports from restaurants, schools, hospital cafeterias, and other places where food is handled, and they found that the order in which inspectors conducted their work did bias the work quality in two ways.
First, they found that if an inspection went relatively poorly, with the inspector citing a relatively high number of violations at a site, that inspector would then apply more scrutiny than usual to their next site—and subsequently cite relatively more violations. However, they also found that if the timing of an inspection threatened to prolong the inspector’s typical workday, that inspector would cite fewer violations than usual.
Ibanez interviewed and even shadowed a number of inspectors throughout their day in order to better understand how they do their jobs.
“They are very dedicated and mindful about following the procedures,” she says. “But in the end, they’re still human. Their behavior is going to be affected by their emotions and their psychology.”
Biases in Food-Safety Inspections
Ibanez and Toffel obtained more than 12,000 inspection reports from Hazel Analytics, which gathers them from local governments across the U.S. This detailed dataset let the researchers track the citation behavior of individual inspectors as they moved from site to site. For each inspector and site, they were able to calculate a baseline rate of violations cited, as well as to observe any significant deviations from this baseline.
“This data is remarkably rich—we can observe both the inspectors and establishments they visit over time,” Ibanez says. This richness allowed the researchers to rule out alternative explanations for their findings.
Their analyses revealed that inspectors were operating under two different cognitive biases.
Inspectors’ Previous Site Matters
First, inspectors’ attitude about the site they are currently inspecting is influenced by what happened at the previous (unrelated) inspection site. Inspectors, the researchers found, bring additional scrutiny to bear when that previous experience was an unusually negative one. In cases like this, when an inspector came from a site with a noticeable number of violations above its past rate, that same inspector increased the number of violations cited at the next site by an average of 8 percent. They call this the “outcome effect.”
The reverse, however, was not true. There was no effect on violations cited when the previous inspection went unusually well.
“When we are using data for making so many decisions, understanding the behavior of the individuals that create that data is something that we can use to improve our analysis—and therefore our decisions.”
“Negative events are generally more salient, dominant, and have stronger effects than positive events,” Ibanez explains. “If an inspector is shocked by a negative trend at one site, they’re going to remember that experience and get harder on the next place they visit.”
Food-Safety Inspectors’ Daily Schedule Matters
The second kind of behavioral bias the researchers observed, however, reduced citations. There were two components to this finding: conducting an inspection that could delay the end of an inspector’s workday decreased the inspector’s level of scrutiny, as did increased inspector fatigue over the course of the day as a result of the inspections they had already conducted. Both of these factors resulted in fewer violations being cited, which the researchers call the “daily schedule effect.”
Inspectors try not to start an inspection without completing it in the same visit, since they would need to spend extra time and money setting up and traveling to the site a second time. So, in order to complete what they start, inspectors can exert some discretion over their working hours.
“They’re free to finish one day’s work a little sooner than usual, and another day a little later, depending on how long the inspections that they were doing that day take,” Ibanez says. Still, inspectors try to preserve a quitting time that they know they won’t run over from day to day.
“If you typically go home at a certain time, you’re going to try to preserve that end-of-shift time,” Ibanez explains. “But because it does not make sense to stop an inspection once it’s begun, it also means that you’re perhaps going to rush a little bit.”
The researchers find that, if inspectors begin an inspection at a time that would mean they would not finish before their normal quitting time, they finish the inspection 4 percent more quickly than usual—and 5 percent fewer violations are caught.
The second part of the daily schedule effect happens as inspectors grow fatigued during busy days. The researchers found that each subsequent hour an inspector conducts inspections during a day results in 3.7 percent fewer citations per inspection that day.
Putting Bias to Work
Rather than claim that food-safety inspectors are falling down on the job, Ibanez believes that her findings suggest ways to help inspectors perform even better than they already do.
For example, the outcome effect—which biases inspectors to exert more scrutiny, which is generally a good thing for public health—could be leveraged by rearranging inspectors’ schedules. Inspectors generally have some discretion over their scheduling, and Ibanez hopes these results help them, and their managers, decide how to sequence site visits.
“What if every time you finished a really bad inspection, you went to an elementary school next?” Ibanez says. “If certain experiences are going to increase an inspector’s detection rate, we should send them to places where that increased scrutiny will be more beneficial for society.”
Meanwhile, the daily-schedule effect could be mitigated by “scheduling inspections earlier in the day, so that the last inspection is always expected to end before a consistent time of their choosing,” Ibanez says. And perhaps by capping the number of inspections an inspector can do on any given day to reduce fatigue.
Either way, Ibanez believes that her research findings about inspectors’ real-world biases can only serve to help public policy.
“These are biases that people don’t notice,” she says. “Understanding them can help individual decision-making.”
And the results extend beyond this one type of job.
“Our work applies not only to food safety, but other types of operations too,” she says. “When we are using data for making so many decisions, understanding the behavior of the individuals that create that data is something that we can use to improve our analysis—and therefore our decisions.”