Operations May 15, 2020
Having a Far-Flung Supply Chain May Lead to More Product Defects
When firms have to collaborate over long distances, the final product suffers.
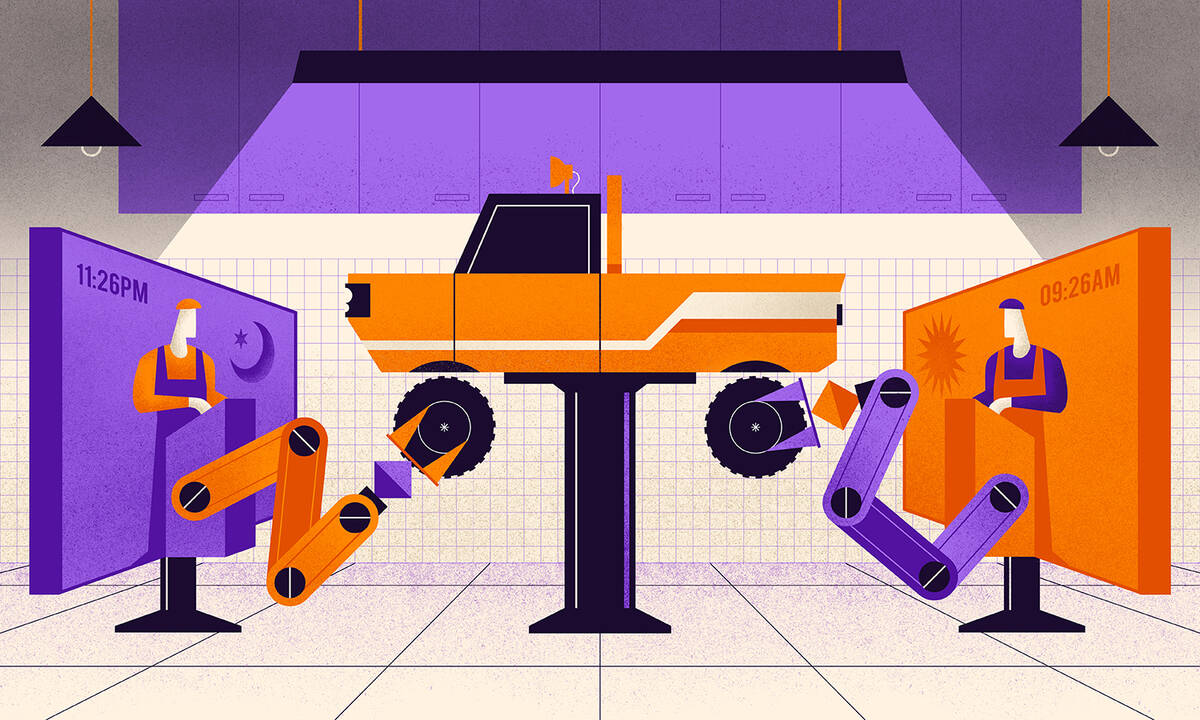
Riley Mann
In this era of globalization, it’s tempting for manufacturing firms to enlist a far-flung network of suppliers for components. After all, labor is often cheaper in other states or countries.
But sourcing parts from distant companies may have hidden costs. In a new study, Rob Bray, an associate professor of operations at Kellogg, and coauthors analyzed the supply chains for more than 600 car models. The researchers found that the farther a component traveled to reach the vehicle-assembly plant, the higher was the risk that consumers would report defects in that component.
Why might distance lead to more defects? For one, designing effective auto parts, and improving them over subsequent iterations, requires that the supplier and assembler communicate and learn about each other’s needs—something that’s easier done face-to-face, Bray says. “Proximity facilitates this learning and helps you get better faster.”
Moreover, some activities, such as exploring a factory, can only be done in person—and these kinds of immersive experiences can make a difference in product quality. Bray argues that an auto-component manufacturer might gain a better understanding of the car model by touching the materials, for example.
“A lot of supply-chain management is really hands-on,” Bray says. “It’s not just a matter of talking things over. It’s actually doing stuff and getting your hands dirty.”
The study’s results could be relevant to other industries, such as pharmaceuticals, where more than just profits are at stake. “If your part fails, people die,” says Bray.
Getting Data on Auto-Part Defects
Bray and his former PhD student Ahmet Colak, now at the Clemson College of Business, got the idea for this study while working on another project about auto recalls. The researchers had obtained data on roughly 976,000 customer complaints about vehicle component failures, collected by the U.S. National Highway Traffic Safety Administration (NHTSA) over two decades.
The data set offered a rare example of product-quality assessments. In most industries, “it’s extremely difficult to get any empirical measure of ‘How good is a product’s quality?’” Bray says. But because the NHTSA is responsible for determining when cars should be recalled, the agency has consistently collected this information.
“A lot of supply-chain management is really hands-on. It’s not just a matter of talking things over. It’s actually doing stuff and getting your hands dirty.”
Then Colak found another database, called Who Supplies Whom, that tracked which auto-component firms supplied which parts for which car models—for example, who produced the rear stabilizers for the 2011 Toyota Corolla or the air duct system for the 2012 A-Class Mercedes-Benz. In all, the database contained information on 1,765 suppliers to 68 auto manufacturers around the world.
Bray and Colak then looked up locations of vehicle-assembly plants and supplier factories. With this final layer of information, they could answer the question: Does the distance that a component travels make a difference in product quality?
For Auto Suppliers and Manufacturers, the Closer, the Better
Bray, Colak, and Juan Camilo Serpa at McGill University used these data to assemble the details on about 28,000 supply chains for 685 car models from 1999 to 2014. They then cross-referenced those data with customer defect reports for each component in the United States.
Parts from faraway suppliers seemed to fare worse, the team found. Increasing the distance by an order of magnitude—say, from 100 to 1,000 miles away—was linked to a 3.9 percent increase in the defect rate. The team estimated that if the typical auto manufacturer replaces its component supplier with the next-farthest one, the defect rate for that component will be expected to rise by 1.5–2 percent on average.
However, this correlation did not mean that the distance had necessarily caused the defects. So next, the researchers put the data through a more stringent test.
They analyzed all cases where an auto manufacturer had moved a factory’s location—motivated, for instance, by tax breaks or other government incentives elsewhere. Such relocations happened 79 times over the course of the study. Sometimes, the factory ended up closer to suppliers after the move, and sometimes the opposite.
“This was kind of a natural experiment,” Bray says. If some factor other than distance was causing the failures, the researchers theorized, then the defect rate should not increase just because a supplier moved further away.
But, as expected, when the distance between the suppliers and auto manufacturer increased, so did the defect rate. And when the distance decreased, the defect rate dropped, too.
And the per-mile effect was three times as strong if the supplier was based in another country than the assembly plant, even if the distance was the same. “A mile domestically is not as harmful as one mile internationally,” Bray says. Why? He speculates that perhaps the road infrastructure in other countries is less developed, making components more likely to get damaged en route.
Why Supply-Chain Distance Leads to More Defects
One reason the researchers suspect that distance might lead to more defects in general: collaborating on component improvements is easier done face-to-face.
To test this hypothesis, they decided to study how much the defect rates for components changed over time. After all, the work of designing and building a car doesn’t end with the first model. Manufacturers continue working to improve product quality with each new version. Thus, if the relationship between distance and quality was due to collaboration, then product quality should have increased faster when the supplier was closer to the assembly plant.
So the team examined what happened to defect rates as auto manufacturers and suppliers collaborated to improve components over time—for example, making improvements to the alternator between the 2012 and 2013 models of the Honda Civic.
“If your phone breaks, it’s fine. But if your brakes fail, that’s not fine.”
What they found supported the collaboration hypothesis: the closer the supplier was to the auto manufacturer, the faster the failure rate for that supplier’s component dropped over subsequent versions. (However, the researchers were not able to rule out other explanations for the relationship between distance and defects—for instance, that auto manufacturers can better judge the quality of nearby firms, and so nearby suppliers tend to be better, all else equal.)
The importance of close collaboration makes sense, Bray says, given the complexity of information that has to be conveyed. “The supplier doesn’t really understand the rest of the car, and the auto maker doesn’t really understand this component,” he explains. “Both of them have partial information.” If the parties are closer together, it becomes much easier to bridge that gap.
Collaboration appeared to be especially critical for certain kinds of cars and components. For instance, luxury cars saw a larger jump in defects as distance increased, probably because they were more complicated and contained more customized parts. The same was true of parts with more subcomponents.
Would Shorter Automobile Supply Chains Save Lives?
While Bray won’t go so far as to recommend that auto companies obtain parts closer to home, he hopes that they see this study as a warning. “I want them to be aware of this additional cost” to product quality, he says.
How much do these small increases in defect rates really matter to car companies? Quite a bit, Bray argues. Given how mature the auto industry is, he says, “getting a 1 percent improvement”—whether in quality or efficiency—“is very difficult nowadays.”
And small gains in component quality can lead to big savings for society, too, since some defective components can lead to car crashes.
Cutting all supply-chain distances in half would reduce collisions by 0.37 percent, his team estimated. When the researchers factored in the crashes’ costs to society, including healthcare and property damage, as well as congestion and pollution from resulting traffic jams, the amount saved worked out to about $2.4 billion per year.
Beyond dollars and cents, Bray reiterates that people’s lives are on the line. “If your phone breaks, it’s fine,” he says. “But if your brakes fail, that’s not fine.”